
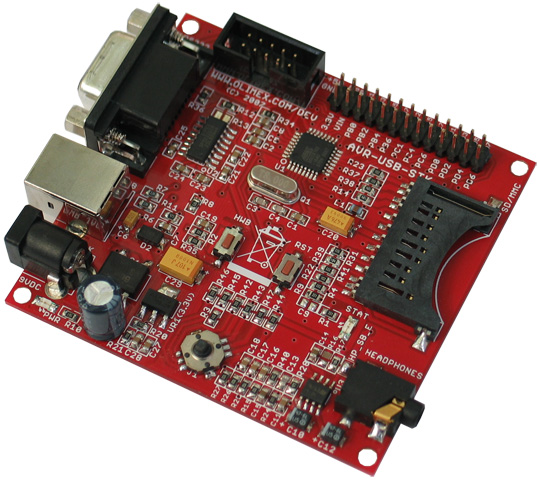
Once this is done, re-home the machine and then re-set the homing direction mask (it should be reversed again since we changed the main direction port invert mask). This is easily remedied by tweaking the direction port invert mask ($3). Right after this you’d typically see that one or more axes are reversed. I then play with the direction homing direction mask ($23) and get it to home in my preferred corner. I usually run a homing cycle and see which direction the axes move. Just be patient and if you’ve wired everything correctly, its bound to work right. You’ll then need to play with the homing direction and main direction port masks (explained below). If you’d like it otherwise, you need to enable HOMING_FORCE_SET_ORIGIN in the config.h file to set 0,0,0 to the homed location and re-upload the firmware. Note that once homing is complete, the entire machine is set in the negative coordinate space. Limit switches must be enabled through homing by setting $21=1 in the settings. Plenty of visual indicators for debuggingĭefault grbl settings The default grbl settings are shown below and assume that your system is belt-driven with a pulley tooth count of 20, 2mm belt pitch and a 200 step/revolution stepper motor that is set to operate in full step mode.Reverse power connect protection protects against errors while connecting the power source.Uses standard 12-24V DC supply and with 12V at 1A and 5V at 2A outputs on the board.Comes with heatsinks for the motor driver chips.Bluetooth control (with an optional HC-05 bluetooth module) to wirelessly connect and operate the machine.USB port eliminates ancient parallel ports and freedom from older expensive machines that are hard to obtain.Limit switches are configurable as active high (normally closed switches) or active low (normally open switches)
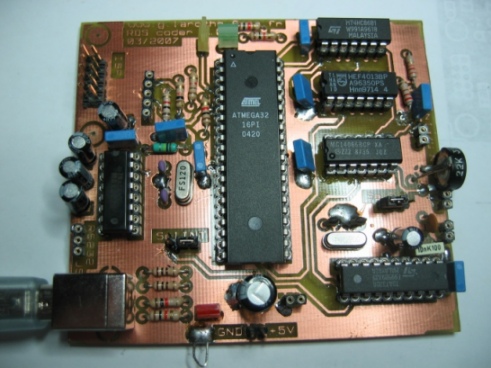
Accommodates upto 6 NO limit switches and almost unlimited NC switches.Options for user configured inputs and feedback such as E-Stop, Reset, Feed Hold, Cycle Start, Homing Location, and Probe.Current limiting can be set independently for every axis including the clone axis.Full step to 32 micro-steps configurable via on board microswitches.Capable of driving upto 4 NEMA 23 motors at 2.2A per motor (with a heatsink, 1.5A without any heatsink).

